Empiece a escribir aquí...
ESTUDIO DE CASO – Frente a costosos errores de inventario, Hidrogística transformó sus operaciones de almacén involucrando a su equipo, estandarizando procesos y construyendo una cultura de propiedad, reduciendo las discrepancias del 5% a casi cero.
Autores: Luis Alfonso Sasmay Subgerente de Proyectos y Servicios; María de la Paz Díaz Jefa de Logística de Hidrogística.
A finales de 2022, Hidrogística, el operador logístico de Aguas Andinas, una de las empresas de agua más grandes de América Latina, se encontró en una encrucijada. Una alarmante discrepancia del 5% en nuestra auditoría de inventario en toda la empresa, equivalente a una brecha de 400.000 €, sacudió nuestra confianza. De esa cantidad, 150.000 euros se confirmaron como pérdidas financieras. Para una empresa que gestiona infraestructuras tan vitales como el agua potable y el saneamiento, estas cifras fueron una llamada de atención.
Estaba claro que teníamos que cambiar la forma en que trabajábamos. En lugar de señalar con el dedo o tratar de solucionar el problema con soluciones rápidas, tomamos una decisión: transformar desde adentro. Fue entonces cuando nos pusimos en contacto con Lean Institute Chile, una conexión que remodelaría no solo nuestra función logística, sino toda nuestra forma de pensar.
En el corazón de nuestro viaje Lean estaba nuestra operación de almacén. El equipo estaba agotado, trabajaba hasta tarde, venía los fines de semana, apagaba incendios constantemente. La mentalidad predominante era que necesitábamos más: más gente, más tecnología, más recursos. Lo que Lean nos enseñaría era que no necesitábamos más. Necesitábamos algo mejor.
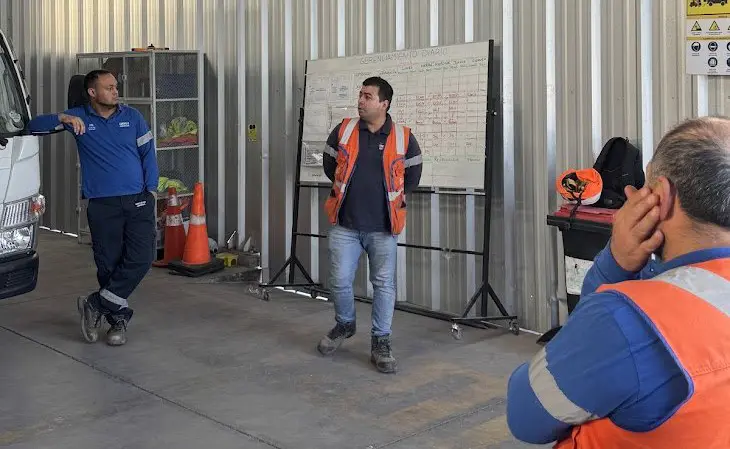
Comenzamos redefiniendo nuestro propósito. Resistimos la tentación de arreglar todo de una vez y, en cambio, optamos por concentrarnos en nuestras discrepancias de inventario. A través del mapeo de procesos, involucramos a todos, desde el liderazgo hasta la primera línea. Juntos, examinamos cada paso de nuestro proceso logístico para comprender dónde se generaba valor y dónde no.
Lo que encontramos fue revelador. Se saltaban pasos básicos como la verificación de los materiales entrantes de los proveedores. Si un proveedor afirmaba entregar 100 unidades, creíamos en su palabra. Esta confianza ciega en el origen estaba desencadenando una reacción en cadena de imprecisiones que se extendían a través de cada parte de nuestro proceso.
Las primeras semanas fueron duras. La gente entró a la defensiva. Muchos creían que los verdaderos problemas provenían de fuera de su departamento. Si no estabas en la habitación, probablemente eras a ti a quien culpaban. Pero una vez que comenzamos a recopilar y compartir datos, esas suposiciones se desmoronaron. La verdad siempre está en los números. Y cuando la gente lo vio por sí misma, cuando se dieron cuenta de que éramos responsables de nuestros propios problemas, las actitudes comenzaron a cambiar.
Los entrenadores Lean del Instituto no actuaron como extraños diciéndonos qué hacer. Se convirtieron en socios. A medida que crecía la confianza, también lo hacía la voluntad del equipo de probar cosas nuevas. Comenzamos a celebrar reuniones diarias, a hacer un seguimiento de los indicadores clave en tableros visuales y a aplicar el pensamiento A3 para analizar las causas fundamentales en lugar de buscar chivos expiatorios.
Creamos estándares de trabajo que antes no existían. Lanzamos un recuento de inventario cíclico diario y lo asignamos a un miembro del equipo recién ascendido del almacén. Esto aumentó tanto la precisión de nuestros conteos como la moral. Activamos el módulo de gestión de almacenes de SAP, sustituimos las notas manuscritas por códigos de barras e introdujimos una segunda capa de verificación en el proceso de picking para evitar que los errores llegaran a nuestros clientes.
Las horas extras, que alguna vez fueron un hecho de la vida, desaparecieron por completo. Ya no necesitábamos quedarnos hasta tarde o venir los sábados para limpiar el caos de la semana. Nuestros procesos funcionaron y los resultados lo demostraron. La siguiente auditoría de inventario mostró una discrepancia del 5%. Al año siguiente, alcanzamos solo el 0,1%. Habíamos pasado de perder 150.000€ a menos de 15€ en diferencias de inventario. Y no contratamos a una sola persona adicional para hacerlo.
La verdadera transformación, sin embargo, no estuvo en los números. Estaba en nuestra mentalidad. Nosotros, como líderes, nos dimos cuenta de que nuestros comportamientos tenían que ser el ejemplo para el resto de la organización y difundir esta nueva forma de pensar en todo el equipo, fue entonces cuando comenzamos a realizar caminatas gemba diarias y a brindar entrenamiento práctico. Hoy en día, ya no reaccionamos ante los problemas; Los estudiamos, los entendemos y los resolvemos juntos.
Este cambio de mentalidad también reconfiguró la forma en que abordamos la resistencia. Al comienzo de la transformación, hubo escepticismo por parte de algunos miembros del equipo. Incluso se consideró el despido de uno de nuestros coordinadores de almacén. Pero en lugar de renunciar a él, nos comprometimos a apoyar su crecimiento. Con un entrenamiento constante y la exposición a los principios lean, no solo cambiaron su desempeño, sino que se convirtieron en un modelo de cambio, ahora defendiendo las mismas prácticas a las que alguna vez se resistieron. Esta experiencia nos recordó que la resistencia no es una señal para retirarse; Es una señal para desafiar la forma en que lideramos.
Nuestro almacén se ha convertido en un punto de referencia para el resto de Aguas Andinas. Incluso Veolia, nuestro accionista mayoritario y líder mundial en servicios de agua, se ha dado cuenta. Lo que comenzó como una solución urgente se ha convertido en una especie de área modelo, en la que estamos desarrollando una cultura de excelencia.
Estos resultados fueron el resultado directo del trabajo de nuestra gente, un equipo que optó por hacerse cargo de sus procesos y comenzó a resolver problemas en lugar de trabajar en torno a ellos. Hemos creado una cultura en la que los problemas no se ocultan sino que salen a la superficie, en la que los datos informan las decisiones y en la que las pequeñas mejoras incrementales son más poderosas que las revisiones drásticas.
No invertimos en nuevos equipos ni en sistemas costosos. Invertimos en nosotros mismos. Aprendimos a hacer preguntas en lugar de hacer suposiciones. Aprendimos a confiar en los hechos, no en las impresiones. Y, sobre todo, aprendimos que el verdadero cambio no comienza con herramientas o software. Comienza con personas dispuestas a ver y liderar de manera diferente. Nuestro viaje del caos a la claridad nos ha enseñado que una transformación lean no tiene que ver con el destino, sino con la disciplina que practicas todos los días.